Commissioning and maintenance of rubber rollers
Jul 30,2021
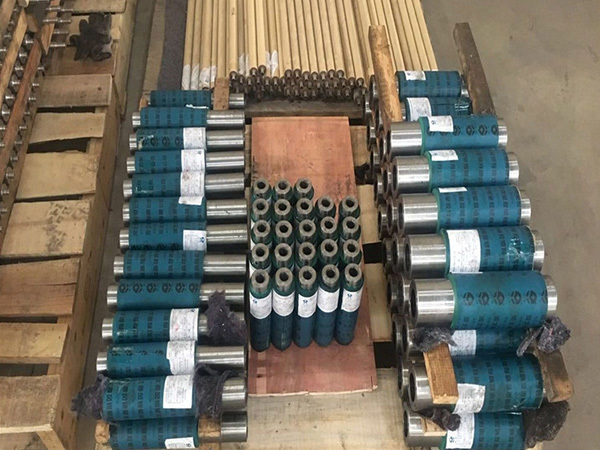
People who have been in the printing industry for a long time know the importance of printing rollers very well. Because it has a direct relationship with the printing plate and is inseparable from the quality of the product, whether you are using an offset press, letterpress press, gravure press or flexo press, you are faced with how to choose and debug tricks. If it cannot be used reasonably and does not comply with its operating procedures, it will not only fail to print an ideal, hard product, but also damage the rubber roller and shorten the service life of the printing plate. Adjusting the printing roller to the advanced level and ideal point is difficult, and it is not something that can be mastered overnight. Since there is no fixed procedure, it relies on long-term production practice to summarize, explore, innovate, and organize a set of advanced printing techniques. Therefore, it is very important to adjust the printing roller.
The following is a comprehensive discussion of the selection, use, commissioning, maintenance and repair of printing rollers.
With the rapid development of the market economy, new equipment, new technologies, new materials, especially new printing equipment, have also emerged. The upgrade is relatively timely, and domestic printing equipment tends to be high-tech, durable and advanced. From the perspective of the international printing industry, data show that some developed countries such as Europe and the United States are still in the forefront of printing equipment. Although the domestic printing industry entered the 90s and introduced many printing machinery and printing equipment from developed countries, when the printing roller needs to be replaced after some years of use, the domestic printing roller is far from the original equipment. Rubber rollers. In the past, printing enterprises set up workshops specializing in the production of printing rubber rollers, which were seriously polluted. With the development of the printing industry and the upgrading of equipment, the traditional old-fashioned printing rollers are gradually eliminated because they cannot meet the needs of high-speed printing machines. Its disadvantage is that it cannot adapt to high temperature and high humidity environment, high temperature softening and low temperature hardening, especially for gold printing and screen printing plates, hindering the improvement of printing quality. In the 80s, there was a major revolution in printing rubber rollers. The new rollers are not limited by climatic conditions, have good strength and corrosion resistance, but the high cost makes small and medium-sized enterprises prohibitive. With the rapid development of the economy, it is still well received by the majority of users.
Debugging and proper use
No matter what type of printing machine it is, after the new equipment is installed, the technician and the neckline machine must first install the printing roller. The installation height of the rubber roller must be adjusted reasonably, and it is indispensable to be in close contact with the ink roller and the printing plate. Printing practitioners know that the height of the letterpress plate is 3.14mm, which is the same height as the font, while the PS version is relatively low, 1.2mm, so pay attention to the roller when installing and adjusting the rubber. If it is a printed matter with a base color, the rubber roller can be adjusted down, and the error ± 0.5mm, so that the ink is transferred from the ink roller to the printing rubber roller more evenly, and the printing rubber roller is reflected on the printing plate. The effect of the print is pleasing to the eye. If this is not the case, ink streaks and ink channels appear.
When printing text, the height of the rubber roller is basically the same as the text plate or slightly lower, so that the printing rubber roller can gently rub the printing plate, so that the text is printed very clearly and cleanly, and the wear surface of the rubber roller is small. It is not easy to damage and can extend the life of the printing plate. Adjustments should be made using a rubber roller. Before use, remove the printing plate and allow the roller to stretch and expand several times. Immediately displays the size of the ink dot on the rubber roller. The operator can determine the height of the rubber roller according to the different needs of printing, and then tighten the top wire. In this way, the height of the roller does not change when printing at high speeds.
If people lack patience when using the roller and are anxious to debug successfully, the following situations will occur:
(A) The surface of the rubber roller is damaged, and the slag is removed, so that the text printing is missing and broken, the text is blurred, and even the phenomenon of flowers and jumping words appears.
(b) Inconsistent text ink, or even text marks without ink color on the surface of the printed matter.
(C) If the rubber roller and the ink transfer rubber roller are adjusted too tightly, it will distort the printing rubber roller, causing economic losses and equipment accidents. The key to offset printing technology is the control of ink channel balance, which relies on the two key components of rubber roller and ink roller, and its quality directly affects product quality. This is especially true for gravure, embossing and flexographic printing.
Generally, printing enterprises must maintain the equipment once a week, including the maintenance of printing rollers. There are several maintenance methods:
1. The rubber roller should be carefully cleaned and cleaned twice a day after the production operation is completed;
2. The cleaning of the printing rubber roller must use specified chemical reagents, such as industrial alcohol, etc., and do not use corrosive solvents;
3. Remove the rubber roller on holidays to prevent deformation under pressure;
4. The protection of the surface of the printing roller is wrapped in newsprint and placed in a ventilated and dark place. In work items, printing rollers usually appear wear, wear, etc. If the new drum is replaced, the cost is too high and the production schedule is affected.
Repairs can be made with rubber patches. Repair process, taking rubber repair agents as an example:
1. Surface treatment: clean, decontaminate, degrease and dry the tentacles that need to be repaired.
2. When repairing rubber, pour group B of rubber repair agent curing agent into the iron can of group A of the main agent, stir quickly and evenly (A:B=1:1), and then pour into the part that needs to be repaired and smooth.
3. Curing: It can be used after curing at room temperature in 4-6 hours, and the maximum strength can be reached within 48 hours.
PREVIOUS:
Contact Us
E-mail:
cfyx@yxrubberroller.com
WhatsApp:
+8613603180655
Address:
No. 369, Fuyang East Road, Jizhou District,Hengshui City, Hebei, China